Our Work
Illuminating Parking for Local Hospital
A south-central Pennsylvania hospital, providing an advanced range of outpatient and inpatient services, was in need of updated lighting within the parking garage utilized by the physicians. RSR Electric recently completed an extensive lighting project in the doctor’s parking garage for this busy healthcare facility.
The main focus of the project was removal of the existing branch lighting circuitry and replacement with a new wire structure. New Galvanized Rigid Steel Conduit (GRC) raceway was installed throughout the three-level structure to accommodate a new lighting layout. By utilizing this system, all cables and wiring will be protected, and future changes to the wiring layout can be accomplished with ease.
Additionally, 145 existing light fixtures were removed, yet reserved for reinstallation within the new lighting plan. The reused light fixtures feature GRC pendant mounts with cast metal boxes for durability. Wall pack lighting was also added to accommodate additional illumination in and around the structure.
An important goal for this project was to minimize impacts for the doctor’s using the garage. In order to keep our work from impeding access to the garage, the RSR team adjusted the work schedule to be on site during off hours, from 7:00 PM to 5:00 AM, Monday through Thursday. This schedule kept our work shifts outside of the busiest hours for the garage. Completed within the owner’s six week planned timeframe, the garage now features updated emergency lighting, general purpose site lighting, and exit signs. The doctors at the hospital can now utilize a well-lit and safe parking structure thanks to the team at RSR Electric.
Our Work
Teamwork Creates Streamlined Efficiency for Distribution of Medication
H & S Industrial and RSR Electric teamed up to help an online pharmacy establish a new efficient workflow to meet the increasing demands of their business. Ordering medications to be shipped directly to the patient’s home has been a resource for many years, providing cost and time savings for the customer. The worldwide COVID pandemic has made this service even more valuable. In order to provide better, faster deliveries without sacrificing important quality control, our client was seeking new equipment to speed up the flow and processing speed for orders.
The project involved removal of an old section of conveyor line from the existing processing line and placement of a new conveyor section, featuring multiple paths to move the medications more quickly through the facility. Additionally, a new shrink wrap machine and scale section were inserted into the process, to streamline the orders for shipment. A camera verification section was also included to reinforce quality control and ensure that the end customer is receiving the correct medication in the correct amounts.
With H & S and RSR working together on this project, we were able to provide a one-stop shop for this client. Our team was involved in the initial budgeting phase to ensure the customer was getting the best value for the equipment that would meet their needs and expectations. Because our team shared manpower there was little downtime between tasks, as everyone helped out where they were needed, keeping the customer’s product lines moving and eliminating delays in their shipments.
Because the project was located a considerable distance from our location in Lancaster County, coordination and planning was required to keep this project on track. Additionally, to limit downtime for the client, a very tight schedule was established to complete the work, including a two-week timeframe to finish the main part of the conveyor. Further challenges encountered during this project involved placing the equipment in a very compact space.
To overcome the hurdles created by the tight space and fast-paced schedule, the team took delivery of the conveyor at the RSR warehouse facility before the project start. This provided the opportunity to inspect the equipment and correct damage that occurred during over the road transportation while verifying the equipment layout. The team then sorted and staged the conveyor, to deliver it to the jobsite in multiple loads, according to a logistical plan, thus eliminating jobsite clutter and allowing a smooth installation. The careful management, open communication, and dedicated teamwork from H & S and RSR delivered the finished project within the tight scheduled timeframe and saved critical time.
The key to success on this project is by far the exceptional teamwork approach between the H & S Industrial and RSR Electric staff. Because our project team worked together so seamlessly, we were able to face any challenge, overcome any obstacle, and deliver the finished product that the customer envisioned. For our team, the ultimate satisfaction is found knowing that we played an important role in helping get medicines out faster to the people who need them.






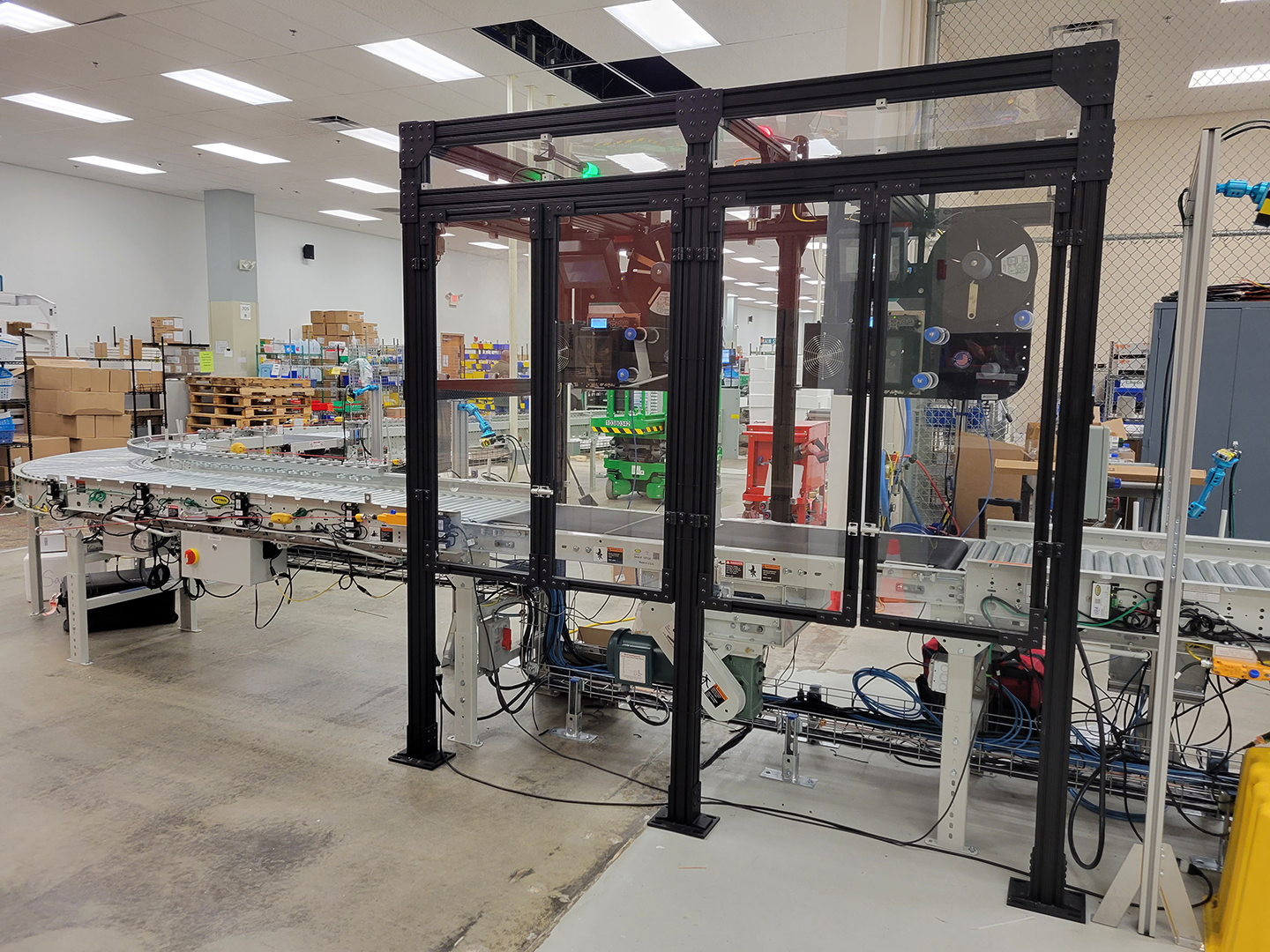
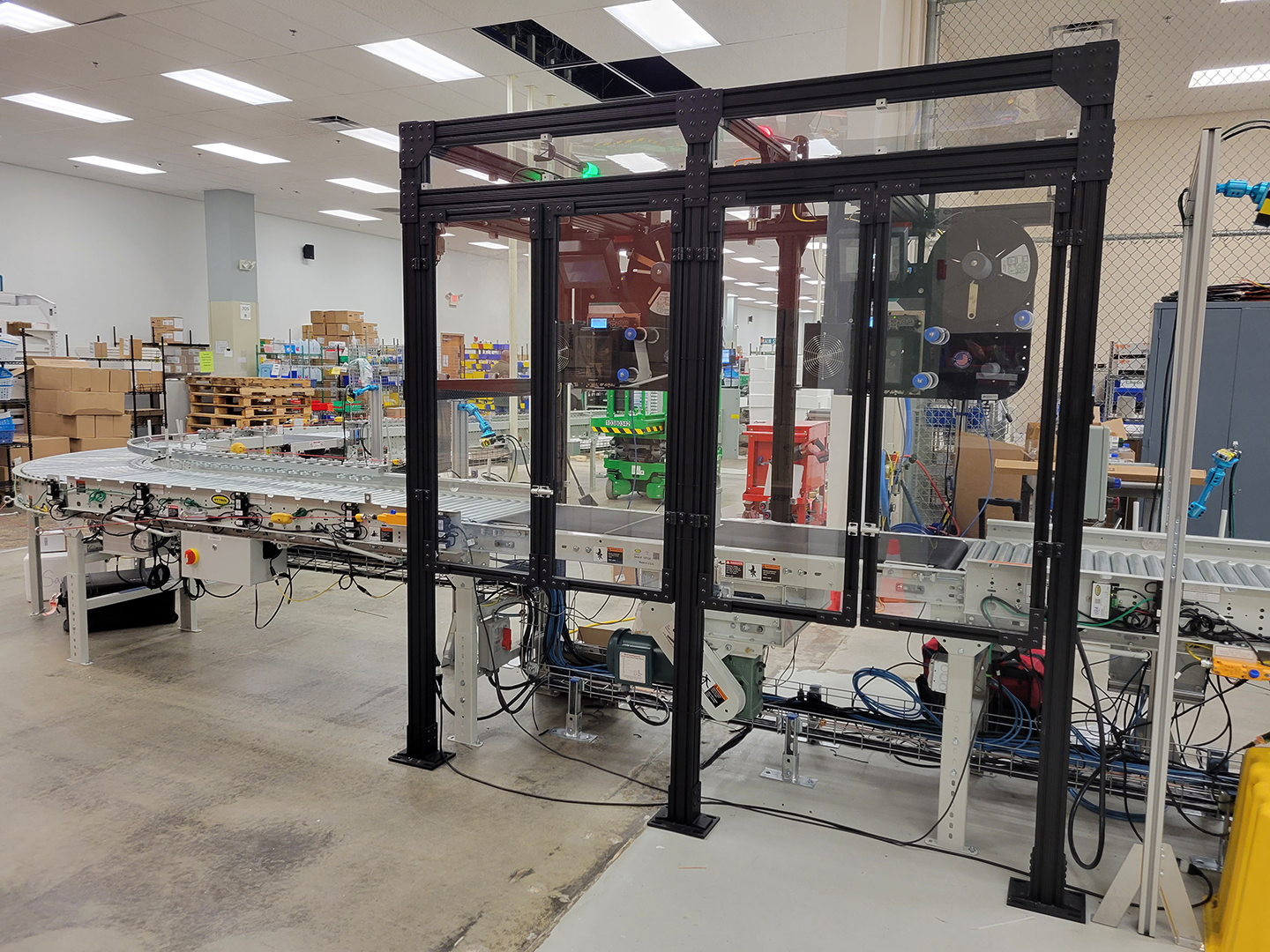


